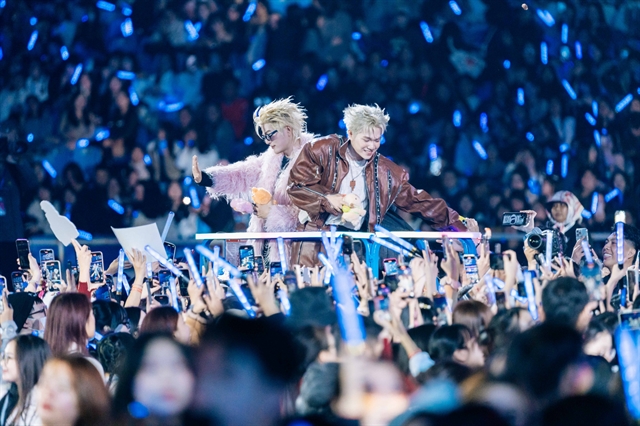
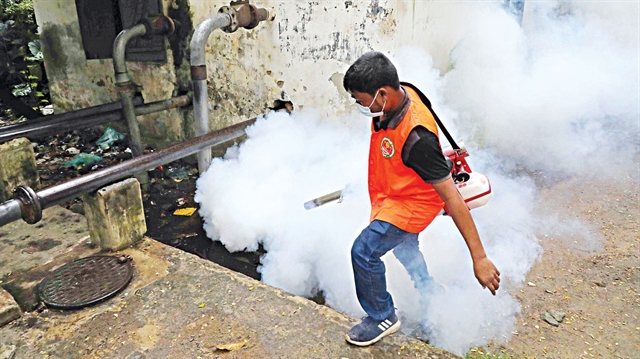
Born and raised in a small village on the bank of Thu Bồn River, potter Lê Đức Hạ started creating items out of clay in the late 1980s, after leaving the army as a volunteer soldier in Cambodia. He now works hard to preserve the craftsmanship of traditional pottery in Viet Nam, with a range of unique designs.
![]() |
Ageless question: A terracotta statue of an old woman.VNS Photo Công Thành |
By Hoài Nam
Like many children, Lê Đức Hạ did not care much for his father’s vocation, although the latter was a famous potter, his porcelain and glaze works winning widespread acclaim.
Born and brought up in a small village on the banks of the Thu Bồn River in Quảng Nam Province, Hạ joined the liberation army when he was very young and was a volunteer soldier in Cambodia when Viet Nam liberated the country from the genocidal Khmer Rouge regime.
After returning, Hạ left home again to make a living via photography shops in Đà Nẵng and Hội An, but the work he’d done earlier, helping out at his father’s workshop, as well as skills he’d learned at fine arts workshops organised in the early eighties by Thăng Bình District’s Glazed Terracotta Co-Operative during the time of State-subsidised economy, tugged at him.
His father – Lê Tuất, had been a rare porcelain craftsman in the central province, and the son realised that he was destined to follow in his father’s footsteps.
“It’s a late story for me. I did not even care for my father’s trade. I just did the jobs I was assigned, including mould designing.
“But the natural-born skills of a potter’s son were enhanced with tips I got from experts at different pottery shops nationwide. Finally, I set up a pottery shop at home,” Hạ said.
![]() |
Yearning: A statue depicting love. VNS Photo Công Thành |
Although he had “inborn” skills, Hạ confessed that his very first batch of products melted because he lacked experience in controlling the kiln’s temperatures.
“I learnt again from my mistakes and restored my kiln, and I was able to use the skills and knowledge I’d gained from experts and elder craftsmen who raised me up. So when my terracotta products (souvenirs and statues) went on sale in Hội An in the late 1990s, they did well.”
He recalled that the ancient town was very quiet in the early days of the đổi mới (renewal) process in Việt Nam in the late 1980’s. Hạ said he spent countless hours creating many attractive designs that tourists could easily carry home.
Trần Thị Tín, 52, a craftswoman in Hạ’s shop, said she’d been working with clay for 18 years.
“My husband and I both worked at the shop as a side-trade, along with rice farming. For us pottery has been one of the most lucrative jobs. Traditionally, rice farming was the major breadwinner, but that changed.
“Almost all the villagers find better paying jobs after rice farming because the financial pressures of raising a family are much higher now. Rice farming can feed us, but pottery is the main source of money for my three children’s education and healthcare," she said.
“We can do all our own work, farming, caring for children, cooking or even trading in the market while being engaged in pottery. The work depends on the schedule of orders and the weather. It takes us one or two days to shape the clay, and we can do work while they dry in the sun before they are baked. It takes at least five days to complete a batch.
![]() |
Shaping things: Potter Lê Đức Hạ decorates a jar in his workshop, Điện Phương Commune, Quảng Nam Province. VNS Photo Công Thành |
Tín said she could earn around VNĐ4 million (US$177) per month – a decent income in a rural village – from pottery, with the income depending on how many products she is able to turn out.
Lê Thị Trang, 44, said almost all the stages in making pottery are done by hand, with only the clay mixing needing a machine.
“We have to be dexterous. We are assigned to different processes including shaping the clay, drying, mould making, trimming, baking and packaging. We get paid on perfect completion of a process and a product that qualifies. And we can reserve time for our children and farming,” Trang said.
Lê Thị Phong, 38, who’s engaged in the trade for 10 years now, said the reliance on weather makes pottery a tough job. For instance, if it rained hard, potters would have to wait till the products dry, before they are shaped further and baked in kilns.
Clay, dug from the Thu Bồn River, is mixed by machine before being poured into a kaolin mould,” Phong said.
“All the clay products have to be baked in firewood and coal-fired kilns for eight hours at an average temperature of 800 degrees Celsius to get perfect pottery products,” she added.
Trần Thu Thủy, 31, said pottery products made in Đông Khương Hamlet were different from those made in Thanh Hà Pottery Village in Hội An and other pottery centres in Việt Nam. She’s been working at the kiln since she was 17.
![]() |
Final touches: A female worker "trims" dried clay lanterns before they are baked in the kiln. VNS Photo Công Thành |
Life trade
Potter Hạ, recognised as an elite artisan by the State in 2013 for his efforts to preserve traditional pottery, said the craft emerged in the area during the reign of the Champa Kingdom (the Champas ruled the central region between 4th and 13th centuries).
“I was told that potteries were often built near areas were clay was plentiful along the Thu Bồn River, and Đông Khương Village was formerly part of the Champa Kingdom,” Hạ said.
“I am fascinated by the Chăm towers, many of which are found in central coastal Việt Nam from Quảng Nam-Đà Nẵng to Ninh Thuận provinces. The colour of pottery in villages along Thu Bồn Village are quite different,” Hạ said, adding that his wife inspired him to become more creative with his craft.
“My wife was in charge of marketing. She encouraged me whenever I did not succeed with a batch. Now we produce around 700 products each month and our pottery is on sale in the tourism hub of Hội An and some shops in Thanh Hà Village,” Hạ said. Some of his clay toys are sold by vendors in Hội An city.
Hạ’s wife died three years ago after struggling against cancer for six years. Since then he has thrown himself into creating new designs, and produces many new ones every month.
![]() |
Scaffolding: Terracotta art works on display. VNS Photo Công Thành |
Passion, creativity
Hạ’s pottery business is also making terracotta products more popular by selling interior and exterior decoration items like garden statues, lamps and ornamental pieces that can be hung on columns and walls.
“Our decorative pottery is a major source of income for potters and villagers, and it helps me remain passionate and creative. I spend most of my time creating new patterns and designs,” Hạ said.
He called a brick house built with the support of architects from HCM City-based Tropical Space company his “termite mound”. The house has been attractively designed with a combination of clay, bricks and timber, with a concrete floor and a glass roof which allows sunlight to flood the space.
“I display my art here, including "intentionally deformed” products – a unique creation in Việt Nam – that Hạ introduced few years ago.
“It was an inspired move. I intentionally crushed jars or statues into protruding or concave shapes, forming extraordinary angles.
“I thought smooth and perfect pottery may not be as attractive to viewers or pottery collectors as something different.
“Childhood and the beauty of women are my major topics. As we get older, memories of childhood get fonder and I want to rewind and go back to that time through my art,” Hạ said.
“It’s an endless love, and you’ll never get bored. It helps you balance art and business.”
Hạ said he had been creating new pottery designs for display at the Huế Craft Village Festival in 2017.
He has so far participated in four consecutive editions of the festival.
His ‘termite mound’ would soon be a rendezvous for children who could have fun with clay, Hạ said. — VNS
![]() |
Abstract pot: A jar with an unusual shape and decoration. VNS Photo Công Thành |
![]() |
Fierce light: A tiger-head shaped lantern.VNS Photo Công Thành |
![]() |
Processing: Lê Thị Trang cleans clay jars and lanterns before they are baked. VNS Photo Công Thành |
![]() |
Out to dry: Wet clay products are dried under the sun before being baked in kilns. VNS Photo Công Thành |