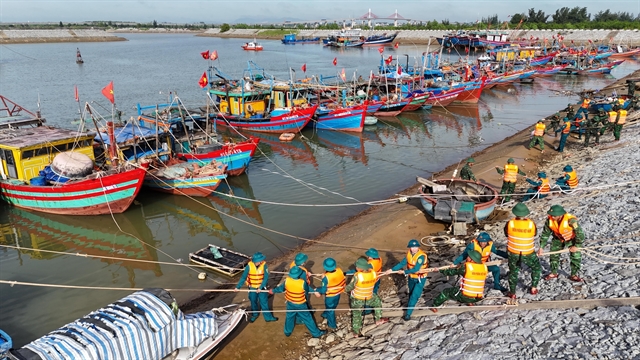
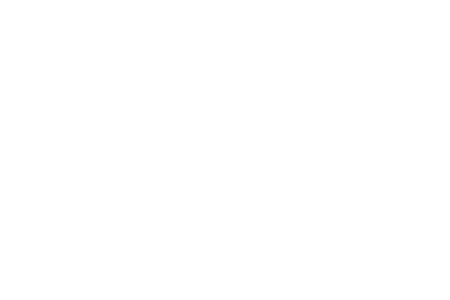
![]() |
Lê Văn Tuấn with his team's machine used to press plates and bowls. VNA/VNS Photo |
ĐÀ NẴNG – A group of students from the Đà Nẵng City's University of Science and Technology have invented a press machine for creating environmentally friendly plates and bowls.
Their invention aims to reduce the widespread use of hard-to-decompose plastic products which pollute the environment and harm ecosystems and human health.
The machine aims to produce bio-degradable products as alternatives to plastic items.
Lê Văn Tuấn, a student in the Faculty of Mechanical Engineering said: “Plastic waste and single-use plastic products are significant pollutants. These products can persist in the environment for decades or even centuries before fully decomposing, causing severe soil, water and air pollution. Consumers today are more conscious of their environmental impact and tend to choose sustainable products to help reduce pollution.”
This trend has led to increasing demand for products made from natural, biodegradable materials, especially for everyday use.
In light of this, the development of eco-friendly products to gradually replace plastic items has become a matter of urgency.
Motivated by this idea, Tuấn’s team, consisting of students of the Faculty of Mechanical Engineering, namely Đặng Hữu Tài, Mai Xuân Sơn, Phan Tấn Sang and Hồ Văn Lý, under the guidance of Dr Bùi Hệ Thống - the faculty lecturer, came up with the idea of making a high pressure machine to form environmentally friendly plates and bowls made from green materials.
According to Thống, researching and designing a press machine to produce plates and bowls from readily available materials like coconut husks, areca sheaths, banana, lotus or almond tree leaves, not only promotes green product consumption but also helps develop a sustainable economy.
These raw materials are easy to find in central provinces, cost-effective and biodegradable, creating an efficient resource recycling cycle, Thống said.
The Eco-Friendly Plate and Bowl Press Machine project not only offers a technological solution but also promotes a green lifestyle within the community, the lecturer said.
According to Đặng Hữu Tài, a member of the research team, the machine’s components include a hydraulic force and control system, a heating system, a pneumatic cleaning system and a UV sterilisation unit.
When the machine is activated, the heating system begins to operate, with the temperature controller increasing the temperature to around 120-180°C for 60-90 seconds, he explained.
Next, the machine cleans the material with high-pressure air blast to remove dirt.
“The material is then shaped by the hydraulic press, with a piston exerting force, cutting and combining with high temperatures. The finished product is then placed in a UV sterilisation chamber,” he said.
Tài shared that the most challenging aspect of the fabrication process was researching the force generation system.
The actual pressing force involves various forces to clamp the material, break the form of it and overcome friction between the material and the upper and lower moulds.
After a period of experimentation, the team opted for a hydraulic control system to optimise the force required to create the finished product.
Thống noted that the machine can be flexibly adapted to produce other consumer products depending on customer demand.
Currently, some farmers and garden owners have shown interest and are looking to place an order.
In the future, the team will continue to develop and improve the press machine to distribute it widely in the market at a price suitable for Vietnamese consumers, he said. VNS