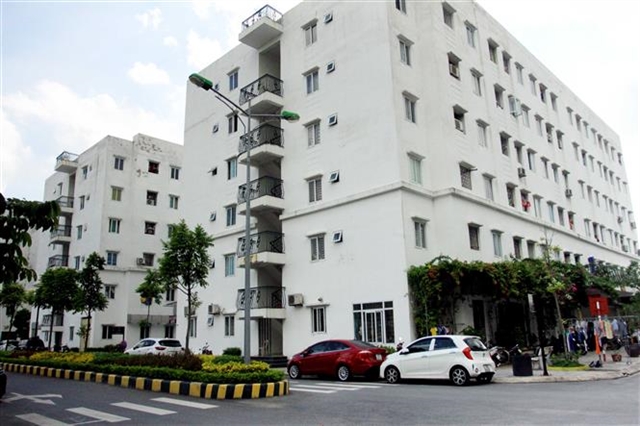
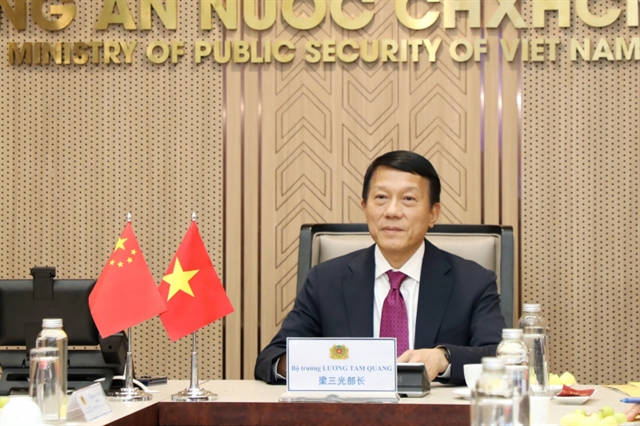
In April 2017, Muto Tadashi waved goodbye to his wife and two sons and left his house in Japan’s Shizuoka Prefecture, where he can see Mount Fuji from his window, to come to Việt Nam, determined to do something to help Vietnamese enterprises.
![]() |
Senior JICA volunteer Muto Tadashi (third from the left) visits TOXECO Packaging and Design Company to check on the implementation of the 5S method. - VNS Photo Hồng Minh |
by Hồng Minh
HẢI PHÒNG – In April 2017, Muto Tadashi waved goodbye to his wife and two sons and left his house in Japan’s Shizuoka Prefecture, where he can see Mount Fuji from his window, to come to Việt Nam, determined to do something to help Vietnamese enterprises.
After 35 years working for foreign and Japanese companies in different positions, Muto wanted to utilise and share his experience with those in need. He has worked as a new product developer, quality assurance manager and manager of a production plant.
After retiring in 2015, he found the Japan International Co-operation Agency (JICA)’s Senior Volunteers programme, which recruits Japanese volunteers aged 40 to 69, “who are motivated by a volunteer spirit and posses practical knowledge and technical skills backed up by their own abundant working experience in a wide range of fields”. He felt immediately that the programme matched his desire to help.
Now a JICA senior volunteer in Việt Nam, 63-year-old Muto has a tiny yet typically tidy working room at the northern port city of Hải Phòng’s Department of Planning and Investment, where he works on ways to help local small- and medium-sized enterprises (SMEs) improve their working environment.
“My mission is to support SMEs in Hải Phòng City to improve quality control and productivity,” he said, adding his support included direct methods such as regular visits, giving consultations and regular checks on progress. He also helps organise seminars and training for companies.
He said that to be selected to get support, enterprises must ensure some certain requirements are met. They must produce products, have directors that show desire for technical support, have staff with the capacity to process suggestions and work in areas related to the volunteer’s specialty.
After receiving a request from an enterprise, Muto will research the company to decide whether or not to lend technical advice or direct support. Sometimes, technical surveys are also needed to make a decision.
With local enterprises seeking support and advice to improve operations, together with recommendations from Hải Phòng’s Department of Planning and Investment, Muto has conducted research on 22 companies with more than 130 visits to local SMEs in the last two years. So far, he has helped 11 SMEs in the city.
Work culture differences
Through his experiences working with Vietnamese enterprises, Muto has found 18 differences in the working culture of Việt Nam and Japan.
The differences vary from the possession and exchange of business cards to organisation style.
“In Japan, the director and managers entrust jobs to subordinates so the subordinates can develop their own ability, take responsibility, implement the jobs and decide by themselves,” he said.
“In Việt Nam, it’s normal for a director to decide all matters and the subordinates follow orders. By doing so, the subordinates are dependent on the director and always waiting for orders and do not decide by themselves,” he said.
Muto pointed out that many enterprises in Việt Nam lack communication inside the company and investment into human development. He suggested Vietnamese enterprises put more value on people.
“The most important thing in a company is the people, those with experiences, knowledge and high motivation to develop a company,” he said.
Muto also suggested an experience- and knowledge-sharing system among labourers.
“In Japanese companies, one’s experiences and knowledge are actively shared with colleagues and newcomers; the company also promotes sharing them as a task for each employee,” he said, “Such experiences and knowledge become the company’s property.”
The 5S method
Through regular visits to the enterprises every two weeks over 10-12 months, Muto has helped select SMEs determine their operational problems and find solutions. He also gives them homework towards Kaizen (improvement). After two weeks of checking on the improvements made by enterprises, they will sit down together to discuss problems and solutions again.
“As the old saying goes, ‘give a man a fish and you feed him for a day, teach him how to fish and you feed him for a lifetime’. I focus on suggesting methods to solve their problems, rather than just giving them a concrete solution,” he said, stressing that teaching a method is better than giving an answer for developing a company.
Introducing the SMEs to the Japanese 5S workplace organisation method – which includes seiri (sort), seiton (set in order), seiso (shine), seiketsu (standardise) and shitsuke (sustain) – Muto said he saw positive responses from local businesses.
“Every company takes our education seriously and works hard to implement the improvements,” he said.
Director of TOXECO Packaging and Design Company Vũ Quang Huy said that after implementing the 5S method under the instruction of Teacher Muto, his company had made significant gains, especially in organising production.
“We used to implement 5S before without guidance and nothing changed at all,” he said.
Being a SME of nearly 50 labourers working in printing, packaging and design, Huy said the workplace used to have papers and boxes lying about in disorder.
“But thanks to the director instructions from Teacher Muto, who stepped in and helped us build organisational charts, visualise the results from our efforts and introduce the 5S method in a very easily understandable manner, everyone from the directors on the board to the end-product workers understands what to do to organise a work space for efficiency and effectiveness,” he said.
For Muto, seeing at SMEs progress as they implement his advice always makes him happy.
“My philosophy of life is to share all the knowledge and experiences I have with others and hope they can be fully utilised,” he said. – VNS
![]() |
The board of directors of TOXECO Packaging and Design Company checks on printed products with a banner calling for implementing the 5S method to create a tidier and more efficient workplace. - VNS Photo Hồng Minh |