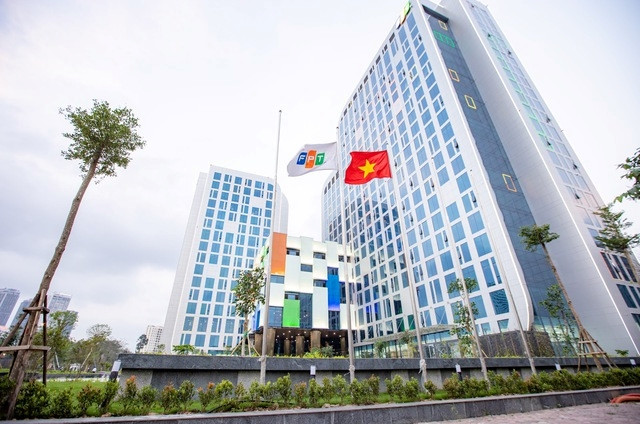
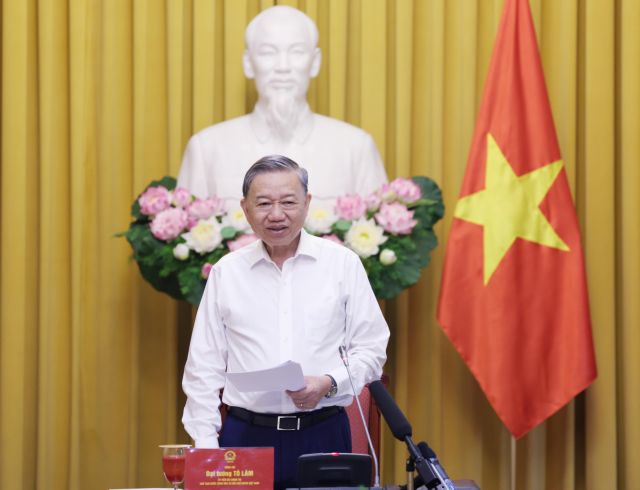
![]() |
Prof. Dr. Lê Hoài Quốc, chairman of the HCM City Automation Association and deputy chairman of the Vietnam Association of Robotics |
The industrial sector is under great pressure and must change and adapt to new trends to expand markets and integrate deeper into the global value chain.
Automation has become of vital importance for companies in it to increase productivity and quality, thus improving their competitiveness.
Prof. Dr. Lê Hoài Quốc, chairman of the HCM City Automation Association and deputy chairman of the Vietnam Association of Robotics, speaks to Việt Nam News reporter Xuân Hương about this and how to promote automation in the country.
How do you assess the use of automation by Vietnamese firms now? In which areas is automation applied the most and what are its benefits?
Along with the development of the industrial, agricultural and services sectors in recent years, automation, which is considered their backbone, has also gradually developed.
Automation has been used to produce food and beverages, pharmaceutical chemicals, personal care products, chemicals, hydroelectricity and thermal electricity, and automobiles, in mining, metallurgy and oil refining and recently in the health and education fields.
Automation has replaced humans in doing simple, strenuous tasks in hazardous and unsafe environments, helping improve productivity and product quality and production and business efficiency, save costs and manpower and steadily boost businesses’ revenues.
This helps enterprises increase their competitive advantage in the international arena.
Automation has become a very important and inseparable part of the modernisation and digitisation of businesses, and is helping develop the country’s economy, HCM City’s in particular.
Understanding the need to develop the automation sector in Việt Nam, especially HCM City, firms based in the city have focused on developing human resources through their own or technology partners’ training programmes to improve the quality of their workforce in the context that many foreign companies are preparing to enter the Vietnamese market.
In the last two years, foreign companies in the field of automation in Việt Nam have been actively transferring technologies to businesses and universities through technical and laboratory equipment assistance programmes.
Siemens signed deals with VNPT, FPT, Vingroup, and Bùi Văn Ngọ Industrial and Agricultural Mechanical Company for factory digitisation. It is sponsoring the automation laboratories at the HCM City University of Technology and Education and the Saigon University of Technology, and has become a technology partner to directly support the HCM City University of Technology.
Mitsubishi is sponsoring the automation lab at the Industrial University of HCM City. Recently the university also set up an industry 4.0 laboratory, with Siemens consulting for its construction and transferring technology.
What are the opportunities and challenges faced by the automation industry amid the development of industry 4.0 technologies?
Applying science and technology, especially automation and mechatronics technologies, in production would help manufacturers reduce production costs, increase in labour productivity, and lower transportation and communication costs, while logistics and global supply chains will become more efficient, and trade related costs will be reduced. As a result, the market for businesses will be expanded.
But according to a survey by the Ministry of Industry and Trade, 61 per cent of Vietnamese enterprises are still not ready for the Fourth Industrial Revolution and 21 per cent of businesses begin to take some preparation steps.
Industry 4.0 will help businesses improve their ability to participate in global and regional value chains. But it is a fact that Vietnamese enterprises do not participate deeply in global value chains due to their use of outdated technologies and the high rate of use of labour, which results in high production costs, lowering their products’ competitiveness.
A lack of skilled human resources in the digital market is another issue faced by local firms in the industry 4.0 era.
Besides, many businesses are not aware of the nature of industry 4.0, fail to remain abreast of technology trends in their industries, are not proactive in accessing technology and, or fail to change their business model to suit the current technology trends.
Vietnamese enterprises suffer from many limitations, but thanks the country’s deeper integration through many bilateral and multilateral free trade agreements and the trend among global firms of shifting investments from China to India and Southeast Asia, automation, which is considered an essential tool in fostering the competitiveness of most manufacturing segments, has a great opportunity for rapid growth.
Do you think current policies for fostering the growth of the automation industry meet the needs of businesses and the market? What should be done to promote automation in key industries to contribute to the country’s industrialisation and modernisation?
Many countries around the world have developed strategies to benefit from this ground-breaking industrial revolution.
The Vietnamese Government has a number of policies to enable the country to immediately participate in industry 4.0.
They include Resolution 23-NQ/TW to develop the national industrial development policy from now through 2030 and Directive 16/CT-TTg for strengthening the ability to approach the fourth industrial revolution with a lot of strategic content requiring concurrent implementation by ministries, industries and localities.
Most Vietnamese enterprises are small or medium-sized, lack capital and technology and have limited production management experience and competitiveness, and therefore to get them to actively participate in the fourth industrial revolution, the Government firstly needs to have policies to help them improve their technological competitiveness to develop new and key products and protect their intellectual property.
Secondly, it needs to support enterprises, especially SMEs, with improving their integration capability so that they can then participate more effectively in global value chains and play a leading role in domestic value chains and industrial clusters.
Thirdly, the education and vocational training sectors need to be quickly reformed towards international integration to develop human resources with appropriate skills for the industry 4.0 era.
Fourthly, it needs to establish an information system with a fully updated database, [information about] the Government’s policies and legal framework, plans for development of sectors and economic regions, programmes and information related to research agencies and organisations, and so on.
Fifthly, it needs to improve communication to raise awareness in society, especially the business community, about the opportunities and challenges posed by industry 4.0.
Businesses firstly need to study advanced industry 4.0 technologies and apply them in their businesses to improve their position in the value chain.
Secondly, they need to promote the development of digital-based production and trading solutions; integrate sensor systems, control systems and communication networks in their business activity and customer care; efficiently use big data based on cloud computing; and collect, analyse and process big data to assist them in decision making and provide a competitive advantage.
Thirdly, they need to develop new skills for each individual as well as the organisation and participate in and efficiently use smart supply chains created by industry 4.0, which are closely linked to the needs of customers.
Fourthly, they must improve the quality of their existing human resources, especially key staff, through training to improve labour productivity, focus on recruitment and have a head-hunting strategy to ensure quality human resources.
Fifthly, they should attach importance to corporate restructuring, review and promptly adjust their corporate governance model [as required], build a streamlined and efficient operating apparatus, and have a workforce with the right jobs and right people to ensure the highest labour productivity.
Sixthly, they need to apply scientific and technological advances in corporate governance, construction, project management, especially research and application of blockchain technology, in their business to improve labour productivity and business efficiency and prioritise co-operation with investors and foreign businesses to improve financial resources and corporate governance capacity and enhance product diversity. — VNS