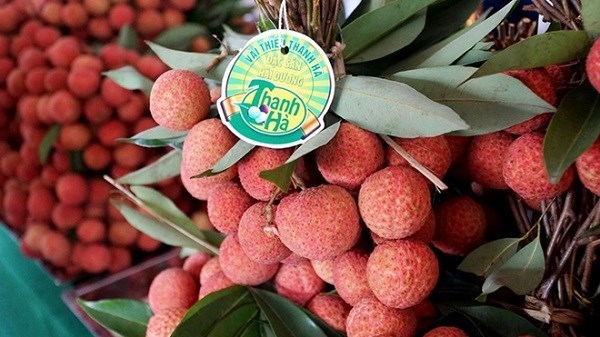
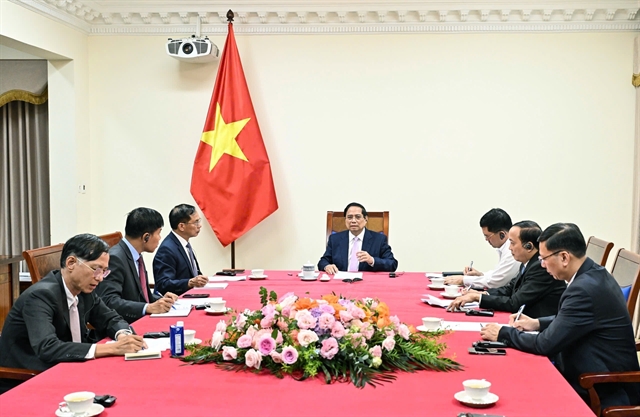
![]() |
Production at Sơn Hà Garment Export Factory in Thanh Hoá Province. Local businesses need huge capital to invest in green production processes. VNA/VNS Photo Nguyễn Nam |
HÀ NỘI — Vietnamese garment enterprises are facing more competition as well as stricter quality and environmental standards in the global market.
According to General Director of the Việt Nam National Textile and Garment Group (Vinatex) Cao Hữu Hiếu, the group has predicted its difficulties of this year since 2022. The group has faced difficulties in two main production fields of yarn and garment.
For yarn production, the difficulties include low demand for yarn in the market, and more competition in the price of yarn after China officially reopened.
Meanwhile, "the garment industry has had only small orders with a few thousand products, and processing price per unit of the garment products has dropped sharply. In addition, delayed delivery by partners has also caused difficulties for businesses in terms of capital and warehousing. Customers also have more strict requirements," Hiếu said.
At the recent annual general meeting of shareholders, the leaders of many textile and garment businesses warned that brands in the global market ask them to reduce production costs and have fast delivery. The brands also have many other requirements relating to sustainable and green development, energy saving and reduction of emissions, while they give just small orders for local businesses.
The requests come from consumer demand in the global market that changes from fast fashion to sustainable fashion, according to the leaders.
Therefore, those factors force businesses to change to participate deeply in the global supply chain. If they do not have investment in high technology, Việt Nam's textile and garment industry will not be able to compete with rivals, like Bangladesh and India for the next three years, said Vice Chairman of HCM City Textile and Garment Embroidery Association and General Director of Việt Thắng Jean, Phạm Văn Việt.
According to the US Green Building Council, Bangladesh is currently home to the most eco-friendly garment factories in the world. Bangladesh's textile and garment industry received US$3.5 billion in foreign direct investment in 2021 mainly for green projects.
Bangladeshi textile manufacturers expect the country's textile industry to account for more than 10 per cent of the global market by 2025 with strong development of green garment products, reported Tạp chí Doanh nhân (Businessmen Magazine).
In an effort to green the textile and garment industry and gain the target of $100 billion in textile and garment exports by 2030, the Indian Government has proposed the establishment of a task force to solve environmental problems in the textile and garment industry. Besides that, there are a series of textile and garment green production programmes.
Local businesses need huge capital to invest in technology renovation and green production processes or build their own brands. It is difficult to do this because up to 70 per cent of enterprises in the garment industry are small and medium sized ones, said Việt.
According to the Việt Nam Textile and Apparel Association (VITAS), most manufacturers in the global textile and apparel supply chain, not only Việt Nam, are receiving requests to meet green standards from big brands.
If not meeting these requirements, there is a great risk of moving orders from Việt Nam to other countries with sustainable textile and garment industries like Bangladesh.
Meanwhile, Việt Nam has also committed to reducing emissions to zero by 2050 at COP26. In the FTAs between Việt Nam and its partners, there are also strict regulations relating to greening that the businesses need to meet.
The VITAS Sustainability Committee sets targets that by 2023 VITAS' textile and garment enterprises reduce energy consumption by 15 per cent and water consumption by 20 per cent, while two textile and garment industrial parks will improve efficiency in electric consumption and water circulation. By 2030, the textile and garment industry will implement green development and build 30 international brands.
The urgent requirements for this industry are greening and digitisation, but capital is a big challenge for the renovation, according to the association.
As of March 31, 2022, total outstanding loans for the textile and garment industry reached about VNĐ150 trillion ($638.8 million), accounting for about 1.5 per cent of the total outstanding loans in the economy, according to the State Bank of Việt Nam.
Of which, the loans for green projects of the textile and garment industry by the end of 2022 were still insignificant because few businesses met the strict requirements for green credit loans.
Meanwhile, VITAS estimates that the industry needs a large capital at about VNĐ500-600 trillion for the green transformation.
Therefore, the industry has proposed the Government to consider reducing interest rates and delay of payment for debt; or having support for the textile and garment enterprises in implementing sustainable development, green transformation and development of a value chain from materials to production and export.
The Power Plan VIII approved on May 15 is also a driving force for local businesses in general and garment enterprises in particular to follow green production.
To solve the challenges, many businesses are actively diversifying markets and products. According to VITAS, they consider increasing exports to a number of potential markets such as the Commonwealth of Independent States (CIS), Latin America, Africa, the Middle East and China.
Meanwhile, many businesses are moving to use more natural and biodegradable materials. Phong Phú Corporation has used environmental impact measuring software at its production facilities to propose the use of materials with low impact on the environment. Vinatex has also deployed yarn management software at its subsidiaries. Việt Thắng Jean has applied ozone technology and nanotechnology in dyeing and adjusting fabric colour. —VNS