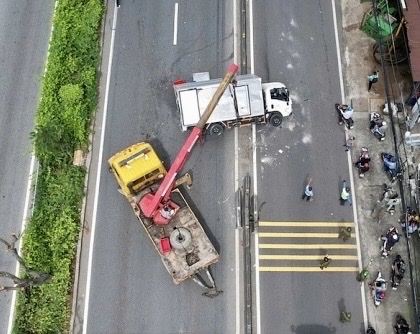

Experts from Japan Productivity Centre and Việt Nam National Productivity Institute have supported 12 companies in the north to improve their employee satisfaction and workplace environment to increase productivity.
![]() |
Representative from Yamaguchi Việt Nam present about implementation of WISE project in the company. — Photo Courtesy of JICA |
HÀ NỘI — Experts from Japan Productivity Centre and Việt Nam National Productivity Institute have supported 12 companies in the north to improve their employee satisfaction and workplace environment to increase productivity.
The two centres have been supporting the companies for the past two years.
This is part of the project for “Improvement of employee satisfaction and work environment”, funded by the Japan International Cooperation Agency (JICA) from May 2016 to April 2018.
The project, also known as the WISE Project, has helped companies identify factors that hinder their productivity and develop solutions to common industry problems.
Almost all the Vietnamese companies, especially small-scale enterprises, are considered to be seriously lacking in practical consulting skills and human resources that could improve business and workers’ welfare.
Under the project, companies are instructed to apply the 5S - a workplace organisation method that uses a list of five Japanese words: seiri, seiton, seiso, seiketsu, and shitsuke. Their translations from Japanese are “sort”, “set in order”, “shine”, “standardise” and “sustain”, respectively.
The list describes how to organise a work space for efficiency and effectiveness by identifying and storing the items used, maintaining the area and items and sustaining the new order. The decision-making process usually comes from a dialogue on standardisation, which builds an understanding among employees of how to work.
Đỗ Văn Dũng, deputy director of Yamaguchi Việt Nam, major producer of auxiliary mechanic, lab equipment and factory supplies, said before joining the WISE Project, the flow of product lines in the company was not effective.
He said the company had no standard, no specific regulations, no training policy, no check-sheet for machine maintenance and no periodic maintenance plan.
He also admitted that previously, communication to staff at the company was not good.
But this changed with the WISE Project, Dũng said.
The company restructured and redesigned the flow of products (for example, raw material, completed product, quality test) so that distances between the stages of production were narrowed, helping save time and labour, and increasing connectivity.
Yamaguchi worker Hà Thị Linh said after learning about and practising the 5S method, workers put office equipment in an orderly manner and the work place became cleaner and brighter.
Trần Đình Trung, a worker of ALS Cargo Terminal at Aviation Logistic, another participant in the WISE Project, said there were visible changes after the project’s implementation. With a clean working environment, everything is easier to find, thanks to 5S, he said.
“For build-up work, I do not have to wait for a forklift or for material as much as before. Jobs are assigned clearly. This has helped increase productivity,” Trung said.
Lê Thị Thu Hương, Administrative and Human Resource Director at ALS, said one of the causes of Việt Nam’s low productivity was that Vietnamese workers carried out tasks quickly but not carefully and meticulously.
Other causes included unreasonable work organisation, lack of funding for updated technology and a training system relying heavily on theory instead of practical skills.
Once the problems were solved, productivity increased, which also led to better income for employees, Hương said, adding if the employees were satisfied with the working environment and income, they would be with the company for further growth.
Kobayashi Ryutaro, a senior representative of JICA Việt Nam Office, said: “Improvement in the work environment and increasing labour satisfaction are very important for Vietnamese enterprises, which are facing limitations in terms of capital, technology and human resource. I do believe that in near future, Vietnamese enterprises will receive high-quality support and consultation by ‘made-in-Việt Nam’ experts.” — VNS