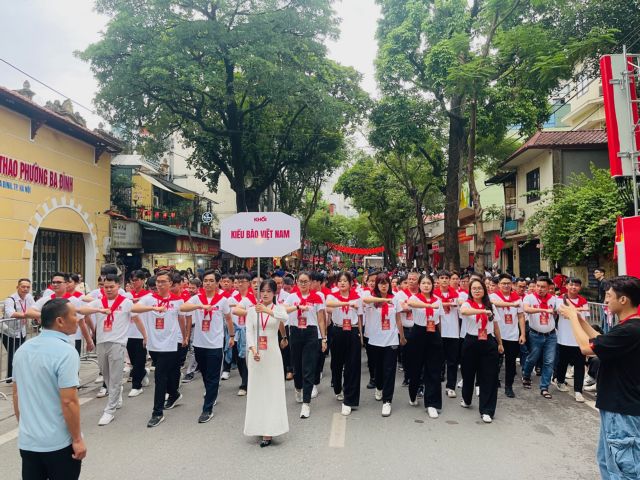
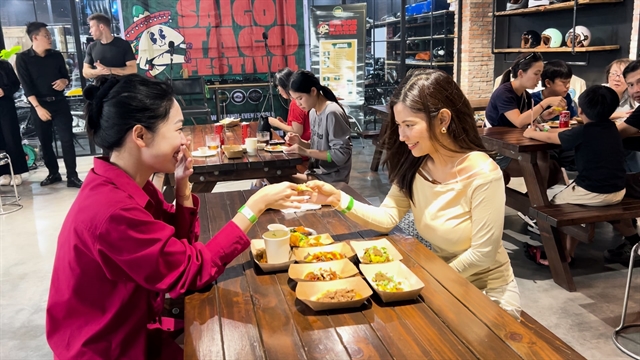
Born and raised in Hà Nội, Lương Thanh Hạnh, 34, started her career as an interior decoration designer, but a love of nature-based traditional silk lured her into an adventure to revive an obscure almost defunct silk village in the northern province of Thái Bình.
By Hoài Nam
![]() |
A weaver makes tussore silk fabrics in the northern province of Thái Bình. — Photo courtesy of Hanhsilk |
Born and raised in Hà Nội, Lương Thanh Hạnh, 34, started her career as an interior designer, but a love of nature-based traditional silk fabrics lured her into an adventure to revive an obscure and almost defunct silk village in the northern province of Thái Bình.
Hạnh first visited the centuries-old tussore silk village of Nam Cao Commune on a trip to her husband’s coastal district of Tiền Hải in late 2011 when most of the weavers had cast off their looms and hand-weaving craft had been fading away for decades.
Despite indifferent feedback from craftsmen in the village at first, for a whole year she insisted on the revival of the silk trade, eventually winning the villagers around.
“They suspected me! The silk village had been left vacant for decades, and some families had even destroyed their looms for firewood. My parents-in-law supported me by gathering veteran craftswomen and arranging silk weaving work for them again,” Hạnh says.
“They (crafts families) agreed to try the basic processes of growing mulberry [the leaves are used to feed silkworms], caring for the silkworms and cocoons, thread spinning and fabric weaving as they had experienced for years previously,” she says.
“The most skilful craftswomen were assigned on quality control. Silk makers used to work from the start to the end of the product but it took time and labour. We devised a work division so that each family was in charge of a certain step in the production process, and helped check each other for the final product.”
![]() |
Silk is dried in the sunlight at a household in Nam Cao commune, in the northern province of Thái Bình. — Photo courtesy of Hanhsilk |
Tussore silk, or coarse silk fabric, is made entirely by hand, so the best silk needs careful quality checking by every family.
The Nam Cao Tussore Co-operative was eventually established, using the modern Hạnhsilk brand for promotions and marketing.
Entirely handmade
Nguyễn Thị Mùi, 65, a silk weaver, says making tussore needs patience and good feeling in the fingers.
“We collect the cocoons after 21 days of feeding the silkworms with mulberry leaves. The cocoons are then boiled for 15 minutes before steaming for six hours. The long heating makes the silk threads more durable,” Mùi says.
“Workers then soak over-boiled cocoons in cold water to remove silk threads, and their skilled fingers are used to tune the thickness of silk threads.”
Mùi, who is the third generation of a weaving family, says that each spinner can only obtain a very small amount of tussore thread, ranging from 70 to 100 grams each day.
Nguyễn Văn Tuế, 68, Hạnh’s father-in-law, supervises the quality control of every process at the commune.
He says the co-operative has expanded the mulberry area to 100 hectares, and set a target of producing at least 100,000 metres of tussore silk fabrics a year.
![]() |
Yellow cocoons are collected from the silkworms in preparation for silk spinning. —Photo courtesy of Hanhsilk |
“We cannot speed up the process because thin silk is easily broken or tangled by careless fingers. Making tussore is a very slow, meticulous and patient process,” he says.
Lê Thị Liễu, 53, who is in charge of spinning silk threads, says the trade would have soon been defunct if Hạnh had not made the trade preservation plan.
She says the ancient craft is seen as a spiritual symbol of the rice farming village, which has been passed down through the generations over the centuries.
“Silk is not only a life making craft, but an honour and a job loved by the village. Our product creates beautiful fashion for all, and we are proud of that,” Liễu says.
The artisan says the silk making even lures the oldest people in the village, with easy manual work, such as reeling silk threads, feeding silkworms or trimming silk.
New era
![]() |
A handloom is used to weave the best tussore silk. — Photo courtesy of Hanhsilk |
Nguyễn Thị Thái, a 60-year-old weaver, says tussore weaving is mostly made by women between the age of 40 and 80. Many families have preserved the trade for three or four generations.
“The sericulture is not hard work. So, 95 per cent of the production is done by women. At least 200 households have joined making tussore in the commune,” Thái says.
Thái says tussore silk can be used for suits, shirts and daily clothing for both men and women.
Fumio Kato, a project leader with the Japanese International Co-operation Agency in Minamibousou City, Japan, suggested that a silk festival in central Việt Nam should build a modern silk trade with unique value, and silk products designed for daily use.
He says traditional silk fabrics should be preserved with new, usable designs for the modern day, while every process of silk making must be conducted meticulously.
Hạnh, founder of the Hanhsilk brand, says tussore silk can be used for daily office fashion, as well as for towels, mattress and pillow covers, scarves, and ties. She says that thousands of Hanhsilk tussore towels are exported to Japan, while the US and European markets account for 50 per cent of her exports.
The Hanoian businesswoman has been exploring the use of natural dye and skills from different silk craft villages to create unique made-in-Việt Nam silk with traditional value and heritage from ethnic minorities in mountainous regions.
![]() |
Tussore silk fabric with jazzy patterns is sun-dried. The rough silk can be used as material for daily fashion. — Photo courtesy of Hanhsilk |
The commune has also been developing an organic-based handmade silk to be part of the One-Commune-One Product (OCOP) umbrella of items.
Hạnh says the greatest value of the commune’s tussore is that it is created from the love, and the skilful hands of craftswomen who have had the knowledge passed down for centuries.
She says she believes that the silk villages of Vạn Phúc, Nha Xá, Phùng Xá, Mã Châu, Tân Châu Mỹ Nghiệp and Bảo Lộc can mix with the handloom weaving and natural dyes used by the ethnic Mông, Tày and Thái to produce excellent, unique made-in-Việt Nam silk. VNS