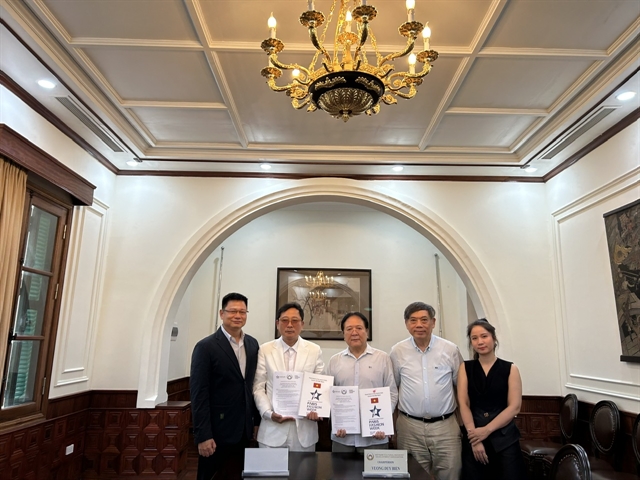
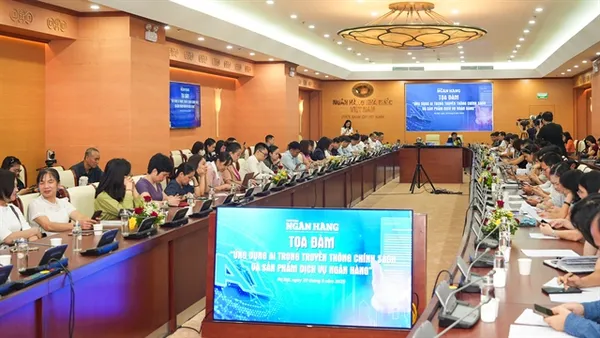
HÀ NỘI - From May to September each year, as the lotus flowers bloom abundantly in the ponds around rural villages in Việt Nam, artisan Phan Thị Thuận from Phùng Xá village, Mỹ Đức, Hà Nội, along with her family, embark on the enchanting process of harvesting lotus stems to weave silk.
Few would have expected that from the slender and rough stems of the lotus plant, it is possible to extract a resilient and beautifully lustrous fibre, sufficient to weave such a exquisite fabric.
The soft, fluffy lotus silk, with its neutral tones, elegant and pure background, reflecting the patient and industrious nature of Vietnamese women, has become the hallmark of this traditional silk village.
Unlike the silk-weaving expertise found in Vạn Phúc village (Hà Đông district), the residents of Phùng Xá commune engage in every aspect of the traditional craft: from cultivating mulberry trees, raising silkworms, and nurturing silk cocoons to weaving and dyeing fabric. From the late 1960s to the early 1980s, Phùng Xá was renowned as the "Silkworm Capital" when the Mỹ Đức Silkworm Company thrived.
With more than 60 years of experience in silk weaving, Thuận is the only artisans in Việt Nam who weaves silk from lotus fibres.
She said: "In our hometown, from grandparents to parents and neighbours in the village, everyone is involved in the silk weaving profession. It's the legacy left by my grandparents, and until now, I've been closely tied to the art of cultivating silkworms and growing mulberry trees."
![]() |
Artist Phan Thị Thuận and her lotus silk scarves. VNS Photo Kiều Trinh |
With a deep passion for the silk-weaving craft, the artisan consistently strives to create new product, aiming to bring fame to their homeland.
She added: "My village has been cultivating silkworms and growing mulberry trees for many years, but when it comes to lotus silk, most people only think of Vạn Phúc village in Hà Đông. Therefore, I want my homeland Phùng Xá to have its own name in the silk industry.
"From there, I struggled with and contemplated on the profession, aspiring to create unique and distinctive products that are incomparable."
With the idea of preserving the enduring beauty and grace of the lotus plant, Thuận spent time researching, experimenting, and successfully innovating the process of harvesting lotus silk and weaving lotus silk fabric. The resulting fabric carries a subtle fragrance, elasticity, quick-drying properties, providing a cool and comfortable feeling for the wearer.
"At first, no one believed I could extract lotus silk and weave fabric from such delicate fibres. I faced numerous failures, but my determination was never to stop," she said.
The production of lotus silk fabric is not a typical manufacturing process but a challenging creative endeavor. To achieve simple yet elegant fabric with a poetic essence, artisans must patiently execute up to 14 meticulous steps requiring concentration and passion.
Lotus stems are harvested, cleaned, and processed quickly to extract more fibres, ensuring bright and soft silk. If left for too long, the stems will dry, and silk extraction becomes impossible.
The most challenging stage is extracting silk from the lotus stem. To obtain lotus silk, artisans must delicately grip each bundle of lotus stems, gently strip the stems by hand, feeling and lightly pulling the fibres, circularly wrapping them together. The fragile fibres gradually appear, thanks to the sensitivity and skilful hands of the artisan.
![]() |
Extracting lotus silk from lotus stems is the most difficult step in the process of making lotus fabric. VNS Photo Kiều Trinh |
To weave a piece of fabric measuring 25cm wide and 1.75-1.8 metres long, an artisan needs around 4,800 lotus stems. Meanwhile, a skilled artisan can only process about 200 to 250 lotus stems per day. So artisans must be patient for nearly a month to extract enough fibres to weave a piece of fabric.
Due to the complexity and sophistication of the production, lotus silk holds high value. Thuận mentioned that she can only produce in limited quantities, catering to pre-order customers. Her lotus silk products have reached many countries such as Japan, France, the United States, Saudi Arabia, Italy, Taiwan and China. Some international customers have even commissioned her to create wedding pillows from lotus silk.
"I will continue to innovate more diverse products and hope that my products will be cherished because lotus silk truly deserves artistic appreciation and admiration," expressed the artisan.
In order to foster connections, facilitate exchanges, and elevate the standing of the craft village, Thuận actively engages in trade promotion fairs, creative exhibitions, and events specializing in "One Commune One Product" items. Committed to imparting her craft to the younger generation, she envisions establishing product showcase outlets, organising skill-teaching workshops for future artisans, and forming her own design team to craft increasingly remarkable and marketable products for both domestic and international customers. — VNS