
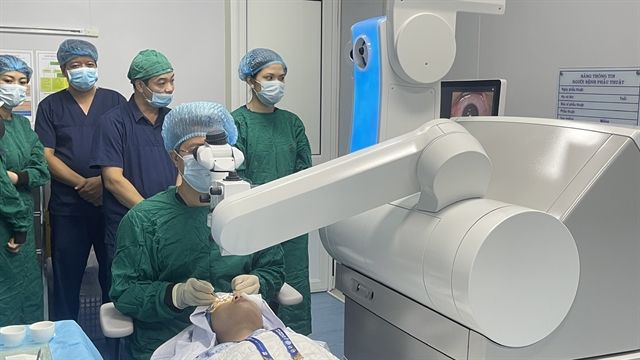
SINGAPORE- Media OutReach - 1 April 2019 - Microsoft Asia and IDC Asia/Pacific today releasedfindings specific to the manufacturing sector for the study, Future Ready Business: Assessing Asia Pacific's Growthwith AI[1].
The manufacturing sector, which contributes to asignificant proportion of Asia Pacific's GDP, continues to face rising competitivepressure due to growing costs and lower margins. Manufacturers are increasinglyturning to emerging technologies to stay ahead of the competition. Those organizationsthat have started to adopt Artificial Intelligence (AI) believe it will nearlydouble their competitiveness (1.8 times) in the next three years.
"Manufacturers in Asia Pacific are slowly, butsurely, seeing the importance of adopting a digital strategy and latesttechnologies. The Study found that 76% of manufacturing business leadersagree that AI is instrumental to their organization's competitiveness in thenext three years,"said Scott Hunter, Regional Business Lead, Manufacturing, Microsoft Asia. "To achievesupply chain excellence, and even develop new business models to addresschanging customers' needs, integrating AI for their business is a must.Organizations which fail to adopt an AI-first strategy risk being left behindin today's competitive market landscape."
"However, 59% of manufacturers have not adopted AI aspart of their business today. This is a worrying sign for the industry thatneeds to thrive on innovation," added Hunter.
For manufacturers that have started their AI journeys,the top three business drivers to adopt AI include higher margins, highercompetitiveness and business agility, as well as better customer relationshipsand outcomes.
They are already seeing business improvements in therange of 17% to 24% today, and further improvements are anticipated in threeyears by at least 1.7 times. The biggest jumps are expected in drivingaccelerate innovation (2.0 times), and higher margins (1.9 times).
Fig 1: AI improves business today and in three years
One example is Piramal Glass, a leading glasspackaging manufacturer in India, which has turned to AI, Internet of Things andadvanced data analytics on the cloud to drive operational efficiency, enhancecustomer experience and generate new revenue models. Their in-house solution,RTMI, offers advanced insights in real-time that led to 5% reduction indefects, 40% reduction in manual data gathering and 25% improvement in employeeproductivity.
"The identifiedbusiness drivers are a clear sign of how technology such as AI can createimproved value by helping organizations gain insights, and better manage theiroperations in a highly complex environment," said Stephanie Krishan, ResearchDirector, IDC Manufacturing Insights. "In fact, according to IDCFutureScape for Manufacturing and Implications for Asia Pacific (excluding Japan), half of the top 10 predictions aredriven by data and AI-centric solutions or use cases, such as creating new ecosystemsfor automation, or even to put data at the center of their processes to drivespeed, agility and efficiencies. This only points towards the fact that thefuture of manufacturing will be built upon data in order to deliver scalableand accelerate growth for the industry."
AsiaPacific's Manufacturers Need to Focus on its Culture, Strategy and DataReadiness
![]() |
Fig2: AI Readiness Model (Asia Pacific's Organizations vs ManufacturingOrganizations)
The Study also evaluated six dimensions contributingto the sector's AI readiness. "The manufacturing sector is lagging behind inCulture, Data and Strategy, compared to Asia Pacific's overall readiness.Business leaders must focus on those areas to stay competitive," said Krishan.
1. Strategy: Manufacturers need to have an AI strategy inplace, and support a more distributed workforce
"By adopting AI industry players will accelerate theirtransformation and enjoy higher benefits. To succeed in an increasingly digitalenvironment, Manufacturers need to have an AI- strategy in place, includingworkforce transformation," said Hunter. Close to half of business leaderspolled see a shift towards a more distributed and flexible workforce due to AIin the next three years.
2. Data: Manufacturers need to work on availability,quality and governance of existing data
There is no surprise that manufacturers need to have amore robust data strategy in place in order to train task-based AI solutions.Today, manufacturers in the region are still dealing with a data structurewhere it can only be accessed by a centralized analytics team. The quality andtimeliness of data are still major issues that are being addressed on an ad-hocbasis. There is also no extensive enterprise data governance program in place.
3. Culture: Traits required for AI adoption lacking inmanufacturing organizations
More than half of the manufacturing workers, andnearly half of the business leaders polled believe that cultural traits andbehaviors are not pervasive in their organization today. For example, 63% ofworkers and 57% of business leaders do not agree that employees are empoweredto take risks, and act with speed and agility within the organization.
"Manufacturers in the region must work on betterintegration of AI into their existing operations, including how data is usedand processed. They need to build an AI-ready workforce that is agile andempowered to innovate," said Krishan. "Only when manufacturers nail down itsstrategy and skills capabilities they can fully harness the full power of AIfor their organization."
Dairy enterprise ACM'snewly opened high-tech milk processing and manufacturing facility in Victoria,Australia is leveraging state-of-the-art intelligent technology to bettermanage costs via a rich data approach. By introducing machine learningcapabilities, ACM is able to reduce human errors from contaminating organicmilk with conventional milk, which also minimizes wastage. In addition, byintroducing automation for production planning, logging and quality assurance;as well as factory maintenance with the help of CRM and AI solutions, ACM hasbeen able to rein in weekend overtime costs of AU$100,000 annually.
Skillsfor an AI-Ready Workforce
The good news is that majority of business leaders andworkers in the sector believe that AI will have a positive impact on theirjobs. 62% of business leaders and 77% of workers believing that AI will eitherhelp do their existing jobs better or reduce repetitive tasks.
![]() |
Fig 3:Perception of AI's impact on jobs (Business Leaders and Workers)
However, according to business leaders, the skillsrequired for an AI future are in shortage. Communication and negotiation skills,entrepreneurship and initiative-taking as well as adaptability and continuouslearning are the top three skills identified in which demand will outstripsupply in the next three years. At the same time, business leaders believe thatthe demand for basic data processing, literacy & numeracy and generalequipment operations and mechanical skills will decrease in three years. Thoseskills are broadly available today, and already now the supply is higher thanthe demand.
The disconnect comes with employers' perception oftheir workers' willingness to reskill. "Business leaders are aware of themassive reskilling efforts required to build an AI ready workforce. However, 22%of business leaders felt that workers have no interest to reskill, but only 8%of workers feel the same. In addition, 48% of business leaders feel thatworkers do not have enough time to reskill, but only 34% feel the same way,"shared Hunter. "Business leaders in this space must prioritize reskilling andupskilling, dedicating employee's time for this to address skills shortage. Evenas it may result in short term productivity impact as building an AI-readyworkforce will result in greater gains in the future."
Microsoftat Hannover Messe 2019
Microsoft will be at Hannover Messe this year at Hall 7, Stand C40 between 1 to 5 Aprilwhere we will showcase how customers, partners are working with Microsoft totransform manufacturing outcomes.
To learn more about how Microsoft is powering thetransformation of the industry, visit https://www.microsoft.com/en-us/enterprise/manufacturing
[1] About the study Future Ready Business: Assessing AsiaPacific Manufacturers' Growth with AI
o Business leaders: Business and ITleaders from organizations with more than 250 staff were polled. Respondentswere decision makers involved in shaping their organization's business anddigital strategy.
o Workers: Respondents screened have anunderstanding of Artificial Intelligence today, and do not play a role indecision making process within their organization.
Microsoft(Nasdaq "MSFT" @microsoft) is the leading platform and productivity company forthe mobile-first, cloud-first world, and its mission is to empower every personand every organization on the planet to achieve more.