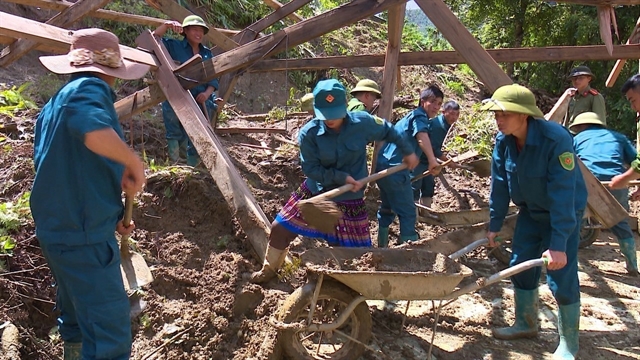
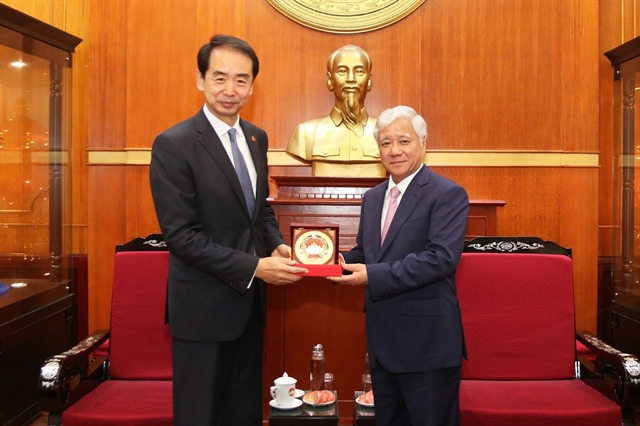
![]() |
Solar panels are installed on roofs of a factory in Việt Nam. More effective solutions and technology transformation are needed to save energy consumption in industrial production. Photo courtesy of SolarBK |
ĐÀ NẴNG — Despite 50 per cent of businesses applying the resource efficient and cleaner production (RECP), savings of fuel and energy consumption per product only achieved a ratio of eight to 13 per cent in 2016-20.
Meanwhile supportive policies in technology transformation and funding for industrial manufacturing companies have yet to help reduce energy use.
An expert from the ministry of industry and trade, Cù Huy Quang, provided the above information at a conference on the 10-year completion of cleaner production in 2016-20 in Đà Nẵng last week.
Huy said in a survey of 5,500 businesses on energy saving applications nationwide, 90 per cent recognised the importance of cleaner production, but only 50 per cent applied methods reducing energy consumption per product.
He said businesses failed to meet the target of saving costs from energy consumption and efficient fuel use in production from 2009-2019.
He said that only VNĐ115.8 billion (US$5 million) including 3.5 million Danish Krone (US$561,000) from Denmark were provided for the 2009-19 cleaner industrial production strategy in 41 provinces and cities.
Huy pointed out that only 34 per cent of 6,000 enterprises had saved five per cent in energy consumption on a product in 2010-15, while only 12 per cent of those manufacturing businesses achieved eight per cent energy saving on a product.
Lê Xuân Thịnh, from Việt Nam Cleaner Production Centre, said technology and boosting recycling in production would help business cut energy use.
He said one tonne of paper needs 100 tonnes of water, and the process will also release 100 tonnes of waste water.
Thịnh said some companies in Việt Nam had applied cleaner production and witnessed positive changes.
He said a paper company in Thái Nguyên invested VNĐ57 million ($2,400) in low cost solutions, but they reaped VNĐ616 million ($26,700) per year in energy savings.
“The solution also helped the company reduce 125 tonnes of carbon emissions, 114,400 cubic metres of waste water and 5.19 tonnes of dust each year,” Thịnh said.
A sugar company in Nghệ An also saved VNĐ4.4 billion ($191,000) per year through technology transformation and efficient process control as well as recycling and reusing water.
He said textile and garment, leather and steel were key industries that need to promote effective energy use.
FOCOSEV joint-stock company – a tapioca starch producer – reduced 1,600 tonnes of solid waste and 3,700 tonnes of carbon emissions each year through a recycling and composting process. It also saved VNĐ3 billion ($130,000) each year through technology and environmentally-friendly solutions.
Đà Nẵng city also saved $433,000 in public lighting consumption by applying nano-lighting technology and saving solutions.
A series of solutions were implemented in the city’s downtown area including dimming, low voltage bulbs and automatic switching off after midnight to save 30 per cent in consumption for each bulb on the street.
The power savings have helped the city cut 12,000 tonnes of carbon emissions per year. — VNS